Напайки на резцы: Токарная оснастка напайки купить, цена в интернет-магазине Вираж
Напайка твердосплавных пластин. | МеханикИнфо
Напайки твердосплавные. Напайка твердосплавных пластин.
Оцените запись
Содержание
- 3-й ЭТАП — НАПАЙКА ПЛАСТИНОК.
- ПРИПОИ.
- ФЛЮС.
- КОМПЕНСАЦИОННЫЕ ПРОКЛАДКИ.
- СПОСОБЫ ПАПАЙКИ.
- НАПАЙКА В ПЛАМЕННЫХ, ГАЗОВЫХ ИЛИ ЭЛЕКТРИЧЕСКИХ ПЕЧАХ.
- НАПАЙКА КОНТАКТНЫМ СПОСОБОМ НА ЭЛЕКТРОСВАРОЧНЫХ АППАРАТАХ.
- ГАЗОВАЯ НАПАЙКА
3-й ЭТАП — НАПАЙКА ПЛАСТИНОК.
Этот этап является наиболее ответственным, так как при неправильном его проведении, во время работы резца, пластинки твердого сплава могут отскакивать или ломаться, вследствие образовавшихся при напайке трещин.
ПРИПОИ.
Припои, применяемые для напайки пластинок твердого сплава, должны иметь температуру плавления на ~ 300° выше температуры, возникающей в процессе резания, сохранять прочность и пластичность при температуре резания, обладать хорошей жыдкотекучестью и обеспечивать быстрый отвод тепла от пластинки твердого сплава к стержню резца.
Рекомендуется применять следующие припои:
Наименование припоя | Состав | Температура плавления | Область применения |
Медно-никелевый (мельхиоровый) | Медь — 68.7% Никель — 27,5% Алюминий — 0,8% Цинк — 3,0% | 1170° | Для работ с большими нагрузками и нагревом режущей части инструмента до 900° |
Электролитическая медь | Медь — 99.9% Примеси — 0,1% | 1083° | Для работ с большими нагрузками и нагревом режущей части инструмента до 700° |
Латунно-никелевый | Медь — 68,0% Цинк — 27,0% Никель — 5,0% | 1000° | |
Латунь Л—62 | Медь — 62.0% Цинк — 38,0% | 900° | Для работ со средними нагрузками и нагревом режущей части инструмента до 600° |
Серебрянный ПСР-45 (ОСТ—2982) | Серебро — 10% Медь — 53% Цинк — 37% | 720° | Для припайки пластинок из высокотитановых твердых сплавов марок Т30К4 |
ФЛЮС.
Чтобы обеспечить хорошую смачиваемость и растекание припоя по поверхностям спаиваемых деталей, для удаления окислов и предохранения от окисления, применяют флюс.
В качестве флюса рекомендуется бура, которую нужно предварительно расплавить, истолочь и просеять через мелкое сито. Хранить буру нужно в закрытых сосудах, предохраняющих ее от влаги и загрязнения.
Бура применяется либо в виде порошка, либо в виде пасты, состоящей из трех весовых частей буры и двух частей вазелина.
Латунные припои паяют с флюсом, который состоит на половину из борной кислоты и на половину из буры. Температура плавления таких флюсов 750 ºС.
При напайке серебряными припоями следует применять флюс, состоящий из 43% фтористого кальция и 57% борной кислоты.
КОМПЕНСАЦИОННЫЕ ПРОКЛАДКИ.
Компенсационные прокладки необходимы для уменьшения термических напряжений. Они возникают при напайке твердосплавных пластинок, различной толщины и размеров, на стержни резцов. Прокладки больших размеров применяют из низкоуглеродистых сортов стали или пермалоя (железо-никелевый сплав). Большим спросом пользуются прокладки при напайке наиболее хрупких высокотитановых твердых сплавов.
Прокладки имеют вид тонкой сеточки или фольги, толщина которых составляет от 0,2 до 0,5 мм. На них имеются отверстия с диаметрами от 1 до 2 мм, расположенные в шахматном порядке.
Компенсационные прокладки имеют несколько достоинств:
Повышают прочность напайки;
Разгружают место спая от напряжений (возникающие при остывании резца).
СПОСОБЫ ПАПАЙКИ.
Нагрев стержня и пластинки и расплавление припоя могут осуществляться следующими способами:
а) в пламенных, газовых или электрических муфельных печах;
б) токами высокой частоты;
в) контактным способом, на стыковых сварочных аппаратах;
г) пламенем ацетилено-кислородной горелки.
Для уменьшения напряжений, возникающих в твердом сплаве при охлаждении после напайки, рекомендуется напаивать высокотитановые сплавы Т60К6 и Т30К4, особенно склонные к трещинообразованию, только по одной опорной плоскости; боковые поверхности пластинки предохраняются от припаивания применением прокладок из слюды или графита.
Напайки твердосплавные. Напайка твердосплавных пластин.
НАПАЙКА В ПЛАМЕННЫХ, ГАЗОВЫХ ИЛИ ЭЛЕКТРИЧЕСКИХ ПЕЧАХ.
Предварительный нагрев стержня.
Головку резца медленно нагревают до температуры плавления буры ~ 800°С.
Подготовка резца к напайке.
Нагретое гнездо посыпают бурой, затем резец вынимают из печи и металлической щеткой очищают образовавшийся жидкий слой шлака на гнезде.
Затем гнездо вновь посыпают бурой, после чего в него устанавливают пластинку твердого сплава, сверху кладут соответствующее количество припоя и вновь посыпают бурой, так, чтобы бура покрыла сплошным слоем припой и всю пластинку.
Эту операцию нужно производить быстро, чтобы стержень не успел охладиться.
Расплавление припоя.
Головку подготовленного к напайке резца помещают в окно печи с температурой 1200° и выдерживают до расплавления припоя.
Прижим пластинки.
Как только припой расплавится и затечет под пластинку, резец быстро вынимают из печи, кладут на подставку, остроконечным стержнем поправляют пластинку в гнезде и плотно прижимают её к опорным поверхностям гнезда. Прижим длится несколько секунд, до затвердения припоя.
Охлаждение резца.
Во избежание резкого охлаждения, ведущего к появлению трещин в пластинке твердого сплава, резец помещают в ящик с крупкой древесного угля или с сухим подогретым песком, где резец медленно остывает.
Значительно лучше резцы, сейчас же после напайки, помещать в камерную печь, нагретую до температуры 250°. Резцы выдерживаются в печи в течение 5—6 часов, после чего охлаждаются вместе с печью.
Очистка резца.
После напайки резец очищают от окалины на пескоструйном аппарате.
НАПАЙКА КОНТАКТНЫМ СПОСОБОМ НА ЭЛЕКТРОСВАРОЧНЫХ АППАРАТАХ.
Контактная напайка производится на стыковых электросварочных аппаратах, которые оборудуются несложным приспособлением, состоящим из 2-х плоских контактных губок, набора торцевых контактов, блока с грузом и педальной кнопки к контактору аппарата. Контакт подводится на 2-3 мм ниже пластинки твердого сплава.
Операция напайки очень похожа на печную и заключается в следующем:
1.Стержень резца зажимается в контактных губках таким образом, чтобы обеспечить возможно большую поверхность соприкосновения торца резца с поверхностью торцевого контакта.
2.Торцевой контакт подводится и прижимается к стержню.
3.Гнездо для пластинки посыпают бурой, а затем путем периодического включения и выключения тока нагревают головку резца до температуры плавления буры (800°). После расплавления буры, металлической щеткой очищают гнездо от окислов и шлаков и опять посыпают бурой; сверху укладывают пластинку твердого сплава, поверх неё припой и сверху опять густо посыпают бурой.ПРАВИЛЬНО. Контакт не касается пластинки твердого сплава
НЕПРАВИЛЬНО. Контакт касается пластинки твердого сплава.
4.Включается ток для расплавления припоя, после чего ток выключается, а пластинка прижимается к гнезду остроконечным металлическим стержнем.
5.Резец освобождается от зажимов и помещается в ящик с крупкой древесного угля или с сухим подогретым песком для медленного остывания.
6.Остывающий резец очищается от окалины на пескоструйном аппарате.
ГАЗОВАЯ НАПАЙКА
При этом способе источником тепла является ацетилено-кислородная горелка. Следует отметить, что этот способ применяется лишь в
случае отсутствия других, описанных выше, источников тепла, либо когда необходимо напаять небольшое количество инструментов.
Пластинка из твердого сплава нагревается с помощью пламени, направленного на стержень резца. В пламени горелки должно присутствовать большое количество ацетилена.
Процесс напайки аналогичен описанному выше печному.
Напайка этим методом должна быть поручена сварщику с достаточным опытом работы.
При любом способе напайки, в результате её, припой в виде тонкой (до 0,1 мм) сплошной пленки должен соединять все поверхности соприкасания пластинки и гнезда.
Пластинка не должна быть смещена в гнезде.
ЧИТАЙТЕ ТАКЖЕ:
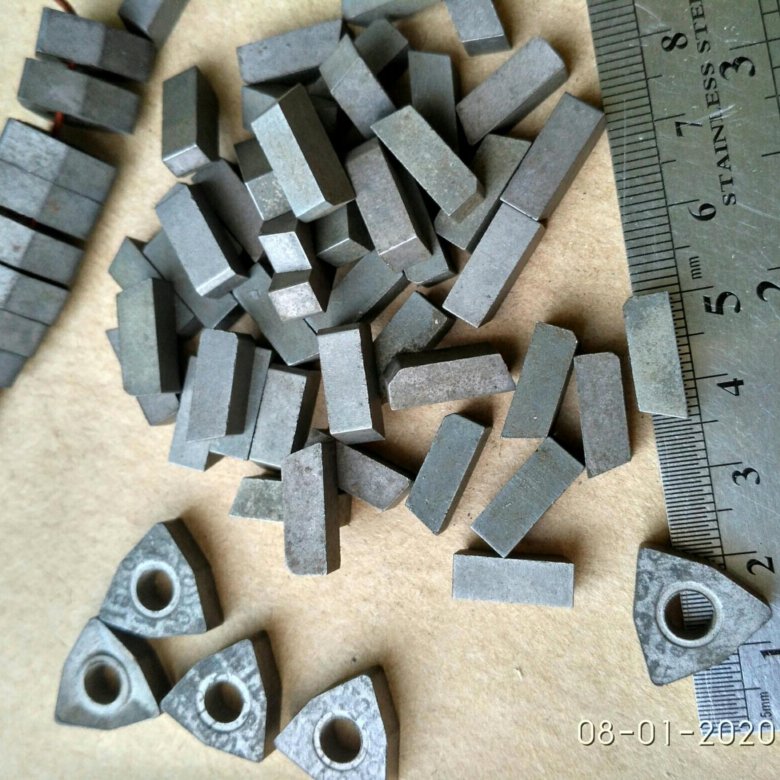
Виды твердосплавных пластин — расшифровка маркировки, обозначений, классификация
Конструкция твердосплавных пластин и их применение
Сменная пластина из твердого сплава — инструмент, который напаивается на резец для проведения механической обработки заготовок. Такие пластины имеют разную геометрию, размеры и производятся из различных материалов. Изделия используются для работы на токарных, фрезерных и сверлильных станках с ЧПУ.
Пластины твердосплавные сменные необходимы:
- для обработки поверхностей заготовок;
- нарезки внутренних и наружных резьб;
- расточки внутренних поверхностей;
- развертки;
- раскроя стекла и цветных металлов;
- выборки канавок, выемок и пазов.
Резец со сменными пластинами
Использование сменных твердосплавных пластин для резцов повышает производительность оборудования, увеличивает скорость проведения операций, гарантирует предсказуемость и высокую точность результата. Резцы со сменными пластинами допускается использовать на высокой скорости, обрабатывать ими твердые материалы и не тратить время на замену режущей части и подточку кромок.
Подробнее о производстве твердосплавных пластин вы можете узнать в этой статье.
Преимущества применения твердосплавных пластин для резцов
Пластины для расточных или отрезных резцов могут быть выполнены из различных марок твердых сплавов, что очень удобно, так как это позволяет иметь целый набор режущих элементов для обработки заготовок из разных материалов.
Использование сменных пластин для режущего инструмента – это еще и экономически выгодное решение, так как в случае поломки или износа нет необходимости заменять весь резец новым инструментом: надо поменять только его режущую часть. Целесообразно использовать инструмент со сменными твердосплавными пластинами и в том случае, если стоит задача автоматизации технологических процессов, что особенно актуально в условиях мелко- и среднесерийного производства, где номенклатура выпускаемых изделий может меняться достаточно часто.
Резцы со сменными пластинами
Среди преимуществ, которыми обладают твердосплавные пластины, устанавливаемые на токарные резцы, следует выделить следующие.
- По сравнению с резцами цельного типа, пластины отличаются невысокой стоимостью.
- Замена твердосплавного режущего элемента не занимает много времени.
- О высокой надежности пластин из твердых сплавов можно говорить даже в условиях интенсивной эксплуатации.
- При необходимости такие сменные режущие элементы можно переналаживать.
- Все современные модели сменных режущих элементов для токарных резцов унифицированы, что дает возможность легко подобрать оптимальный вариант для определенного типа обработки и марки металла заготовки.
Благодаря применению сменных твердосплавных пластин с механическим креплением значительно увеличивается срок службы державки токарного резца, отпадает необходимость в осуществлении таких вспомогательных операций, как заточка режущей части и ее пайка. Что важно, при использовании такого режущего инструмента снижение температуры и силы резания может составить 40%. Благодаря характеристикам твердых сплавов, которые используются для изготовления пластин, с помощью последних можно выполнять обработку металла, изменяя режимы резания.
Некоторые виды форм твердосплавных пластин для резцов
Современной промышленностью выпускаются различные типы сменных пластин, изготовленных из твердосплавных материалов. Требования к параметрам каждого из этих типов оговорены в соответствующих государственных стандартах.
- ГОСТ 19086-80 определяет характеристики пластин режущего, опорного типов и стружколомов.
- ГОСТ 19042-80 оговаривает требования к классификации, форме и системе обозначений сменных пластин из твердосплавных материалов.
- ГОСТ 25395-90 распространяется на твердосплавные пластины типов 01, 02, 61, 62, которые фиксируются на державке токарного резца при помощи напайки. Требования этого нормативного документа распространяются на элементы, которые соединяются при помощи напайки с резцами расточного, проходного и револьверного типов.
Ознакомиться с ГОСТ 19086-80 «Пластины сменные многогранные твердосплавные» можно ниже:
Плюсы и минусы сменных пластин по металлу
Твердосплавные пластины для токарных резцов имеют больше преимуществ, чем недостатков.
- Прочность. Для изготовления пластин используют карбид вольфрама, кобальт, титан. Эти материалы гарантируют высокую стойкость инструмента на износ и стабильность при перепадах температур.
- Экономия. Если износилась напайка цельного резца, державку обычно тоже выбрасывают. У резцов с механическим креплением твердосплавных пластин достаточно только повернуть кромку, а когда износились все кромки — заменить пластину. Сам резец служит гораздо дольше сменной пластины, при аккуратном использовании его практически невозможно сломать.
- Универсальность. Достаточно одного резца и набора сменных пластин, покупать несколько инструментов разных размеров и геометрии нет необходимости.
- Стандартизированные размеры и формы.
Пластины твердосплавные изготавливаются по ГОСТу и имеют стандартные размеры и формы, что особенно важно при работе на станках с ЧПУ.
- Быстрая замена затупившейся режущей части. На замену изношенной пластины уходит минимум времени, оборудование не простаивает, как это бывает при переточке и подгонке напайных элементов.
- Простое использование. В обозначениях токарных сменных твердосплавных пластин легко разобраться. Маркировка поможет понять, для какого резца предназначена оснастка, какие материалы ей можно обрабатывать и на какие обороты выставлять станок.
Минус у сменных пластин один — дороговизна, которой есть объяснение: изделия изготавливаются из высокопрочных сплавов и отличаются продолжительным сроком службы, поэтому не могут стоить дешево.
Классификация токарных резцов по металлу: твёрдосплавные, со сменными пластинами, легированные
Обработка металлов на токарном станке заключается в придании детали нужной формы методом снятия лишнего материала с заготовки. Операция выполняется резцами различных видов, приспособленных под определенную процедуру. Больше всего существует видов токарных резцов. Далее вы узнаете, какие они бывают и чем отличаются.
Конструкция токарного резца
конструкция токарного резца
Условно можно разделить любой резец по металлу на два элемента: головку и державку. Головка — это исполнительная часть, которая состоит из нескольких плоскостей и режущих кромок, заправленных под определенными углами. В зависимости от характера обработки материала подбирается и угол заточки.
Державка необходима для фиксации резца в держателе токарного станка. В срезе державка представляет собой прямоугольник или квадрат. Существует несколько стандартных размеров сечений каждой формы.
Различают следующие конструкции токарных резцов:
- прямые — державка и рабочая головка располагаются на одной или параллельных осях;
- изогнутые — державка согнута, если смотреть на нее сбоку;
- отогнутые — рабочая головка инструмента изогнута по отношению к державке, если смотреть на нее сверху;
- оттянутые — ширина головки меньше, чем державки.
Головка может находиться на одной оси с державкой или быть смещенной относительно нее.
Классификация токарных резцов
Согласно общепринятой классификации ГОСТ все токарные резцы по металлу делятся на следующие категории:
- с режущей кромкой из легированной стали — весь инструмент выполнен из единого куска металла. Они могут изготавливаться и из инструментальных типов сталей. На сегодняшний день используются редко;
- с твёрдосплавными напайками — рабочая твёрдосплавная кромка-пластина приварена к основе — головке. Это наиболее распространенный тип инструмента;
- с фиксацией твёрдосплавных пластин механическим способом — режущая пластина фиксируется на головке с помощью винтов, прижимов. Сменные твёрдосплавные пластины изготавливают из металлических и металлокерамических материалов. Это самая редкая категория.
Существует классификация и по направлению подающего движения:
- левые — подаются слева: если взять его в левую руку, основная рабочая кромка располагается под большим пальцем;
- правые — подаются к станку справа: если взять в правую руку, основная рабочая кромка будет под большим пальцем, более распространены на практике.
Классификация твердосплавных пластин
Твердосплавные пластины для токарных резцов классифицируются по ряду параметров.
- Тип инструмента. Токарные резцы бывают канавочными, фасонными, отрезными, подрезными, расточными. Для каждого инструмента требуются пластины разного профиля.
- Материал. Свойства твердосплавных пластин для токарной обработки зависят от того, в каком количестве в сплаве присутствует титан, вольфрам и другие компоненты. Изготавливают сменные пластины и из керамики. Такая оснастка подходит для обработки жаропрочных сплавов и непрерывной чистовой и получистовой обработки металлических заготовок.
- Размер. Твердосплавные пластины выбирают под размер обрабатываемых заготовок.
- Величина заднего угла. Этот параметр влияет на то, насколько чисто будет обработана заготовка. Чем больше задний угол, тем чище обработка. Пластины с большими задними углами применяют обычно для резания мягких металлов.
- Класс точности. Выпускаются токарные сменные твердосплавные пластины 5 классов точности.
С их помощью обрабатывают изделия с разными допусками в зависимости от геометрических параметров заготовки.
Преимущества использования токарных пластин
Пластины для отрезных либо расточных резцов производятся на основе разных марок твердых сплавов. Это весьма удобно, поскольку позволит вооружиться большим набором режущих элементов, которые будут обрабатывать заготовки из разных элементов.
А еще применение сменных токарных приспособлений для режущего инструмента можно уверенно назвать выгодным решением с экономической точки зрения, поскольку, если случится поломка или износ, не нужно будет менять весь резец целиком, только лишь его режущую часть. Лучше всего применять инструмент, оснащенный сменными твердосплавными пластинами, тогда, когда требуется автоматизировать технологические процессы. Это особенно важно при мелком и среднесерийном производстве разных изделий.
Твердосплавные изделия, которые ставят на токарные резцы, имеют ряд своих преимуществ:
- они стоят дешевле по сравнению с цельными резцами;
- заменить твердосплавный режущий элемент на новый можно очень быстро;
- пластины на основе твердых сплавов обладают высокой надежностью даже при интенсивной эксплуатации;
- если нужно, то подобные сменные режущие части можно переналаживать;
- все существующие модели данных режущих элементов для резцов унифицированы, поэтому можно без труда подобрать подходящий вариант для того или иного типа обработки, а также марки материала обрабатываемой заготовки.
А еще использование сменных твердосплавных пластин, оснащенных механическим креплением, можно значительно повысить срок эксплуатации державки токарного резца, а также не потребуется затачивать и паять режущую его часть. Кроме того, в условиях применения данного инструмента температура и сила резания может снизиться до 40 процентов. Твердые сплавы обладают такими свойствами, что их можно применять для производства пластин, а с их помощью можно обрабатывать металлы при условии изменения режимов резания.
В настоящее время выпускаются разные виды твердосплавных изделий. Требования к каждому типу прописаны в государственных стандартах. Они представлены ниже:
- ГОСТ 19086–80 — подразумевает характеристики опорных и режущих пластин, а также стружколомов;
- ГОСТ 19042–80 — прописывает требования к форме, классификации, а также к системе обозначений пластин сменного типа на основе твердосплавных материалов;
- ГОСТ 25395–90 — регулирует производство твердосплавных пластин нескольких типов, их фиксируют на державке резца посредством напайки.
Это касается элементов, соединяющихся напайкой с резцами револьверного, проходного или расточного типа.
Маркировка твердосплавных пластин
Маркировка твердосплавной пластины информирует о материале изготовления, форме, величине заднего угла, длине режущей кромки и классе точности оснастки. Буквы и цифры в обозначении всегда расшифровывают слева направо.
Расшифровка маркировки твердосплавной пластины
Каждый символ в маркировке обозначает конкретный показатель. Первая буква дает информацию о форме твердосплавной пластины, вторая — о заднем угле, третья — о допусках по высоте, толщине и размеру вписанной окружности, четвертая — о наличии стружколома или отверстия.
Следом за буквами перечисляют цифры. Первыми двумя обозначают длину пластины, двумя следующими — толщину, двумя последними — радиус углы. Последние две буквы характеризуют тип стружколома или его отсутствие (в этом случае вместо двух букв пишут None). Последнее обозначение (две буквы и четыре цифры) говорят о сплаве, из которого изготовлена токарная сменная твердосплавная пластина.
Перейдем к обозначениям.
Форма пластины
Может быть абсолютно разной, от ромбовидной с углом при вершине 35 градусов до круглой. Пластины разной геометрии придают обрабатываемой детали разные свойства.
- H — шестигранная 120°.
- O — восьмигранная 135°.
- P — пятигранная 108°.
- R — круглая.
- S — квадратная 90°.
- T — треугольная 60°.
- C — ромбовидная 80°.
- D — ромбовидная 55°.
- E — ромбовидная 75°.
- M — ромбовидная 86°.
- V — ромбовидная 35°.
- W — треугольная 80° с увеличенным углом при вершине.
- L — прямоугольная 90°.
- A — параллелограмм 85°.
- B — параллелограмм 82°.
- N/K — параллелограмм 55°.
Некоторые формы твердосплавных пластин по металлу
Задний угол пластины
Пластины режущие твердосплавные используют для снижения усилия, прилагаемого при наружной и внутренней обработке.
- A — 3°.
- B — 5°.
- C — 7°.
- D — 15°.
- E — 20°.
- F — 25°.
- G — 30°.
- N — 0°.
- P — 11°.
- O — специальный угол.
Класс точности
Подразумевает допуски на теоретический диаметр вписанной в пластины окружности, толщины и других параметров. Допуски важно учитывать для пластин до подготовки кромки и нанесения покрытия.
Конструктивные особенности пластины
Описывают форму пластины: наличие или отсутствие крепежных отверстий, наличие одной или двух рабочих сторон, наличие или отсутствие стружколомающей геометрии.
Размер, толщина, радиус
В маркировке твердосплавной пластины цифрами зашифрованы:
- первые две цифры — длина режущей кромки;
- вторые две цифры — толщина пластины;
- третья пара цифр — радиус скругления при вершине.
Дополнительные обозначения
Дополнительно указывают тип исполнения пластины (правое, левое, нейтральное) и параметры режущей кромки (острая, со скруглением, с фаской).
Стружколом
Маркировка стружколомов разнится от производителя к производителю. При выборе следует опираться на рекомендации из каталога.
Конструкция
Токарный резец составляют две конструктивные части: державка, с помощью которой инструмент садится в посадочный паз станка, режущая головка. Держатель выполнен в прямоугольной или квадратной форме, является главной частью приспособления.
Головка состоит из заточенной под необходимым углом кромки и нескольких плоскостей, является рабочей частью приспособления, в процессе обработки придает заготовке требуемую форму. Угол заточки влияет на то, как снимет резец металл с заготовки.
По конструкции резцы разделяются на несколько видов:
- прямые: державка, рабочая головка расположены на одной оси, или на двух параллельных;
- изогнутые: при рассмотрении сбоку видна изогнутая державка;
- отогнутые: рассматривая инструмент сверху, отчетливо виден изгиб рабочей части;
- оттянутые: ширина державки больше рабочей, оттянутой влево или вправо, головки.
Оси обеих частей детали при этом совпадают или смещены.
Выбор режущей пластины при обработке различных металлов
Выбирать твердосплавную пластину для токарного резца требуется с учетом следующих факторов.
- Материал заготовки, которую необходимо обработать.
- Вид обработки — черновой съем, чистовой и финишный проход, получистовая обработка.
- Размеры, радиус и класс точности пластины. К примеру, для черновой обработки нужно брать пластину с большим радиусом и небольшим классом точности.
- Форма и марка пластины, подходящие под имеющийся резец.
- Ширина канавки и пластины (для отрезной и канавочной пластин).
- Профиль, тип резьбы, правое или левое исполнение, шаг резьбы (для пластин, предназначенных для нарезания резьбы).
Резец с механическим креплением
Важно!
Для резцов некоторых производителей подходят только оригинальные твердосплавные пластины. В частности это касается отрезных и фрезерных изделий, а также пластин для сверл. Оснастка для точения чаще всего универсальная и совместима с державками разных брендов.
Важные требования для успешной стоматологической пайки
В зуботехнической лаборатории пайка является необходимой частью работы. Благодаря широкому спектру применения пайка сохранила свою актуальность в стоматологических технологиях, несмотря на развитие современных процедур сварки и склеивания. Ежедневное количество процедур пайки в зуботехнической лаборатории по-прежнему намного превышает количество других методов соединения.
В этой статье вы можете найти полезную информацию о том, как добиться успешного результата пайки.
Что такое пайка?
Пайка является наиболее распространенным процессом соединения металлических компонентов, и принципы, лежащие в его основе, не изменятся в будущем. Припой — это расплавленный присадочный металл, который используется для соединения металлических деталей. Температура обработки присадочного металла ниже точки солидуса соединяемых сплавов. При пайке припой смачивает, но не плавит эти сплавы.
При производстве стоматологического оборудования часто используется пайка. Большие частичные протезы обычно изготавливаются из частей и спаиваются вместе после тщательной подгонки к мастер-модели.
Каковы шесть требований для стоматологической пайки?
Полное понимание материалов, используемых в процессе пайки, и их надлежащего применения являются важными составляющими осторожного подхода к пайке.
1. Совместимость с металлами
Припой, используемый в процессе пайки, должен иметь температуру обработки, соответствующую спаиваемым сплавам. Стоматологический припой должен быть устойчив к среде полости рта и иметь состав, сравнимый со сплавляемыми сплавами. Это означает, что для успешного паяного соединения требуется металлургическая совместимость и равные коэффициенты теплового расширения припоев и сплавов.
2. Очистите металлические поверхности
Контактные поверхности должны быть очищены от жира и окислов, что может быть достигнуто с помощью шлифовки или пескоструйной обработки.
3. Предварительно подогретые компоненты каркаса
Для достижения достаточной текучести и оптимального смачивания сплава соединяемые компоненты каркаса должны быть соответствующим образом нагреты. Температура в месте пайки должна быть выше температуры обработки припоя, но не выше температуры солидуса сплава.
4. Смачиваемость
Если припой обладает отличными смачивающими свойствами, он будет равномерно растекаться по сплаву, смачивать обе поверхности и заполнять зазор при пайке. Он образует капли, если припой имеет низкую смачиваемость. Припой не течет, и в этом сценарии не происходит диффузии; другими словами, соединения металлов в сплаве и припое не соединяются.
5. Флюс для растворения оксидов
Флюс растворяет соединения кислорода на поверхности сплава. Флюс поглощает оксиды в процессе растворения и предотвращает дальнейшее окисление.
6. Параллельные стенки зазора для пайки
При снятии давления припой вдавливается в зазор для пайки только в том случае, если стенки компонентов каркаса параллельны друг другу. Стенки должны быть облицованы шириной от 0,05 мм до не более 0,2 мм с равным расстоянием между ними.
Если вы ищете
Надежная зуботехническая лаборатория Vitality Technologies — это зуботехническая лаборатория с полным спектром услуг, обслуживающая стоматологические кабинеты по всей стране. Мы специализируемся на имплантации зубов, несъемном протезировании, высококачественных съемных протезах и многом другом.
Запишитесь на бесплатную онлайн-консультацию, чтобы узнать больше о наших услугах и ценах.
Почему пайка по-прежнему важна в стоматологической технике
Как часто вы паяете? Вы когда-нибудь задавались вопросом, насколько важна пайка в общем контексте работы зуботехнической лаборатории и какие требования необходимы для достижения успешного результата пайки? Если да, то вы можете найти эту справочную информацию полезной. Отправляйтесь с нами в путешествие по прошлому, настоящему и будущему (стоматологической) техники пайки!
Пайка: незаменима в зуботехнической лаборатории
«Пайка» как метод соединения является важным аспектом повседневной работы в зуботехнической лаборатории. В стоматологической технике пайка используется уже более ста лет, однако метод пайки известен гораздо дольше. Пайка практиковалась еще в древности. Методы пайки тех дней включали медную руду и помогали ювелирам создавать сложные ювелирные изделия.
Пайка является наиболее распространенным методом соединения металлических материалов, и принципы, на которых основан этот метод, не изменятся в будущем.
Несмотря на современные методы сварки и склеивания, пайка не утратила своего значения в стоматологической технике из-за ее универсального применения. В зуботехнической лаборатории ежедневное количество процессов пайки по-прежнему явно превышает количество других методов соединения.
Что такое пайка?
Пайка — это процесс соединения металлических деталей с использованием расплавленного присадочного металла, известного как припой. Температура обработки присадочного металла ниже точки солидуса соединяемых сплавов. Припой смачивает эти сплавы, но не плавит их во время пайки.
В процессе пайки жидкий припой и твердо-горячие сплавы подвергаются процессу взаимной диффузии. Прочность соединения (= качество диффузионной структуры) и устойчивость к коррозии являются решающими факторами для долгосрочного успеха паяного соединения.
Припои: необходима устойчивость к среде полости рта!
В стоматологической технике используются только твердые припои, так как очень важна устойчивость к среде полости рта. В дополнение к предварительным припоям (основным припоям) доступны специально разработанные постприпои (вторичные припои), имеющие более низкие температуры обработки.
Припои подразделяются на тугоплавкие припои с диапазоном плавления от 950 до 1200 °C и низкоплавкие припои с диапазоном плавления прибл. 700 и 900 °С. Различные диапазоны плавления подходят для разных целей. Важно, чтобы припои и сплавы были совместимы друг с другом. Для получения надежного паяного соединения требуется высокая степень осторожности. Понимание материалов, используемых в процессе пайки, и знание того, как их правильно применять, являются частью тщательного подхода к пайке.
Ниже приведены наиболее важные требования для успешной стоматологической пайки:
1) Совместимость металлов
Припои, выбранные для процесса пайки, должны иметь температуру обработки, подходящую для спаиваемых сплавов. Стоматологические припои должны быть устойчивы к среде полости рта, а их состав должен быть аналогичен составу припаиваемых сплавов. Это означает, что (металлургическая) совместимость и близкие коэффициенты теплового расширения припоев и сплавов являются предпосылками для получения надежного паяного соединения.
2) Эффективная смачиваемость
Способность припоя эффективно смачивать сплав является еще одним требованием для успешного процесса пайки. Если припой обладает идеальными смачивающими свойствами, он равномерно распределяется по сплаву, смачивает обе поверхности и заполняет паяный зазор. Если припой имеет плохую смачиваемость, он образует капли. При этом припой не течет и не происходит диффузии; или, другими словами, соединения металлов, содержащиеся в сплаве и припое, не смешиваются. Идеальная диффузионная структура образуется, если разница между температурой обработки припоя и точкой солидуса сплава минимальна.
3) Чистые металлические поверхности
Чистота поверхностей припоя является основным требованием для адекватного смачивания. Контактные поверхности должны быть очищены от жира и окислов. Для подготовки контактных поверхностей для пайки можно использовать шлифовку и/или пескоструйную обработку.
4) Флюс, растворяющий оксиды
Рекомендуется использовать флюс для предотвращения образования оксидов. Флюс растворяет соединения кислорода на поверхности сплава. В процессе растворения флюс поглощает оксиды и предотвращает дальнейшее окисление. Процесс пайки следует завершить сразу после нанесения, так как растворимость оксидов, захваченных во флюсе, ограничена.